Injection molding is a production method that involves pumping melted material into a mold, or mold, to manufacture components. Metallurgy, die-casting, glassware, silicones, confectioneries, and most typically flexible and thermoplastic plastics are among the substances used in injection molding. To use a helical screw, the metal for the component is supplied into a heated nozzle and pumped into a die cavity, where it helps to cool and solidifies to the cavity’s structure.
Injection molding produces a wide range of elements, from substances to whole automotive body sections. Some basic injectable molds may be made utilizing advancements in 3D printing technology, which employ liquid resin that does not meltdown during the additive manufacturing of some relatively low thermosets.
Injection molding is a piece of unique equipment that consists of three components: an injection device, molds, and clamps. Pieces must be correctly constructed to help the injection molding process go more smoothly; the fabric used for the component, the intended form, and characteristics of the piece, the substance of the mold, and the qualities of the molding machine must all be considered. This diversity of engineering concerns and opportunities contributes to injection molding’s adaptability.
Process Characteristics
Injection molding involves forcing liquid plastic or latex materials into a mold cavity using rams or screw-type ejectors; the substance hardens into a design that conforms to the contours of the mold. It is most typically used to handle both thermoplastic and thermosetting, with the former having a far larger volume of application.
Injection molding is the process of injecting a high-pressure raw material into a mold that molds the polymeric into the required shape. 14 Moulds might have one cavity or several holes. Each chamber in a multiple aperture mold might be similar, forming the same components, or distinct, forming numerous diverse designs in a single process. Appliance injection molding has benefitted from this technological advancement giving birth to several worthy applications.
Advantages of Injection Molding
Different materials, particularly numerous forms of plastic and multiple colors, can be used simultaneously. Because of the high pressure that the castings are subjected to throughout the process, it is possible to design and construct elaborate and complicated geometrical forms.
The process is repeatable, resulting in regular product quality because the process is heavily machine-oriented, labor expenses are low. Waste plastic is reground and re-used inside the technique, resulting in an ecologically friendly method with minimal waste because produced pieces have a more-or-less completed look, they require little maintenance following the ejection.
Let us look at some of the applications of Injection molding
1. Robotics
In today’s plastics business, mobile robots are employed in many aspects of the manufacturing cycle, particularly the molding process. From putting materials into injection molded parts machines to finalizing and integrating injection molded products, robots give plastics producers a significant advantage by boosting productivity and ensuring superior value.
Machine tending is the most typical use, which involves unloading completed components from an injection molding machine so that they may be processed further. Due to the heat-sensitive documents being molded, the conventional manufacturing process is labor demanding and needs high consistency in operations. Robotics may relieve workers of routine work and reduce the risk of injury, leading to better product uniformity and manufacturing capability.
Furthermore, optimizing the conclusion of a plastic manufacturing line may significantly improve production levels and reduce costs. Robots can relieve people of arduous and repetitive physical labor like packaging, labeling, and palletizing, while also allowing for better packaging, warehousing, and transportation.
2. Medical & Healthcare
Plastic injection mold is a cost-effective and convenient means of making high-precision, high-accuracy, and high-quality medicinal products. From biomedical devices to lab equipment and diagnostic equipment, it’s utilized to make things.
Plastics are now widely used in modern industrial processes, thanks to advancements in material industrial methods and skills. Plastics are frequently utilized in conjunction with the injection molding technique to design variables and complete units of medical product and gear parts in the pharmaceutical industry sectors. Injection-molded plastics have progressively contributed to decreased contagious illness rates, improved pain control, and cheaper medical expenditures as innovative polymers and element layouts are produced.
Tiny, elevated parts found in diagnostics test kits, like the lateral flow in-vitro diagnostic cartridges, are frequently manufactured using plastic injection molding methods.
3. Toys
When you stroll down any company’s toy section, you’ll observe that many of the toys are manufactured entirely of plastics or produce a large amount of plastic injection molding pieces. In the toys and novelty sector, plastic injection molding is a standard method. In comparison to products manufactured of other metals or timber, toys made of plastic pieces have several benefits.
Toys manufactured of plastic give consumers not only a vast range of size and design options, but also high intensity, light and airy, colorful adornment, inventive concepts, designing with precision, increasing the speed of mass production, material, color, and finish flexibility, waste minimization.
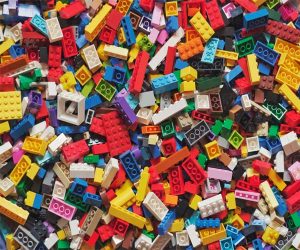
Millions of toys are made each year, resulting in billions of dollars in sales, making the toy sector one of the most plastic manufacturing industries. The toy business has supported the development of very inventive processes such as plastic injection molding, which has aided in the development of increasingly sophisticated toys. As new toys need the capacity to perform specific activities and have more moving components, plastic injection molding has gotten increasingly complex.
The Parting Words
Because of its lightweight, consistent chemical qualities, powerful insulating capabilities, and low price, plastic has increasingly displaced many metal materials in high-end businesses and everyday life. Polymer materials, which represent novel materials, have been one of the four primary fundamental materials at this time (steel, wood, cement).
Farming, industrial, healthcare, aviation, automobile, and construction sectors all employ them. The plastics business is growing at a breakneck pace. Injection molding allows for the development of a wide range of complicated forms, sizes, and precision plastic items. Short cycles, ultimate efficiency, and high accuracy are all advantages. With technology, plastic is also evolving and soon it will be ubiquitous.
Leave a Reply